انواع سیلندرهای پنوماتیک و نکات مهم در انتخاب هر سیلندر
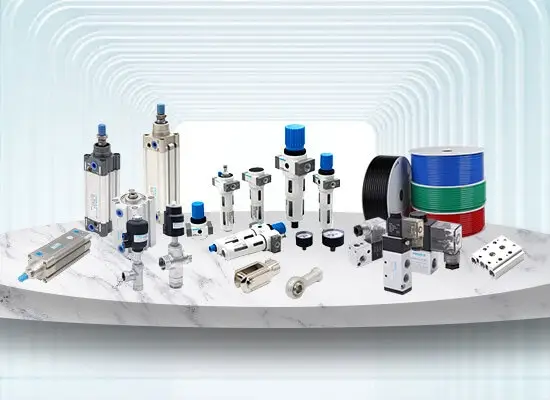
سیلندرهای پنوماتیک از جمله اجزای مهم در سیستمهای پنوماتیکی هستند که برای تبدیل انرژی هوای فشرده به حرکت مکانیکی استفاده میشوند. این سیلندرها در بسیاری از صنایع مانند خودروسازی، بستهبندی، رباتیک و ماشینآلات مورد استفاده قرار می گیرند. در این مقاله به بررسی انواع سیلندرهای پنوماتیک، مواد ساخت، استانداردهای تولید و فرمولهای محاسبات نیرو وسرعت خواهیم پرداخت
. انواع سیلندرهای پنوماتیک
سیلندرهای پنوماتیک به انواع مختلفی تقسیم میشوند که برخی از مهمترین آنها عبارتند از:
سیلندرهای تککارا (سیلندر پنوماتیک یک طرفه): این سیلندرها تنها در یک جهت حرکت میکنند و بازگشت به حالت اولیه با استفاده از یک فنر داخلی یا نیروی خارجی انجام میشود
سیلندرهای دوکارا(سیلندر پنوماتیک دو طرفه ): این سیلندرها در هر دو جهت حرکت میکنند و هوای فشرده برای ایجاد حرکت در هر دو جهت اعمال میشود
سیلندرهای تلسکوپی: این سیلندرها دارای چند مرحله داخلی هستند که امکان افزایش طول حرکت را فراهم میکنند.
سیلندرهای چرخشی( اکچویتور پنوماتیک ): این سیلندرها برای ایجاد حرکت چرخشی به کار میروند و در کاربردهایی مانند دربهای خودکار و دستگاههای پیچبندی استفاده میشوند
استانداردهای تولید سیلندرهای پنوماتیک
استانداردهای تولید سیلندرهای پنوماتیک برای اطمینان از کیفیت و قابلیت اطمینان این تجهیزات بسیار حائز اهمیت هستند. برخی از استانداردهای مهم عبارتند از:
ISO 15552: استاندارد بینالمللی برای سیلندرهای خطی پنوماتیک.
ISO 6431: استاندارد مشابه با ISO 15552 که به استاندارد DIN 24335 نیز شناخته میشود.
VDMA 24562: استاندارد انجمن مهندسان مکانیک آلمان برای سیلندرهای پنوماتیک.
NFPA/T3.6.7: استاندارد انجمن ملی حفاظت از آتش برای سیلندرهای پنوماتیک در ایالات متحده.
فرمولهای محاسبات نیرو و سرعت محاسبات نیرو و سرعت در سیلندرهای پنوماتیک
فرمولهای محاسبات نیرو و سرعت محاسبات نیرو و سرعت در سیلندرهای پنوماتیک برای طراحی و انتخاب صحیح این تجهیزات بسیار مهم است.
1-محاسبه نیرو: نیروی تولید شده توسط یک سیلندر پنوماتیک به فشار هوا و سطح مقطع پیستون بستگی دارد. فرمول محاسبه نیرو به صورت زیر است
F=P×A
که در آن F نیرو (نیوتون)، P فشار هوا (پاسکال)، A سطح مقطع پیستون (متر مربع) هستند.
سطح مقطع پیستون میتواند با استفاده از قطر پیستون (D) محاسبه شود
A=¼πD2
محاسبه سرعت: سرعت حرکت سیلندر پنوماتیک به دبی جریان هوا و سطح مقطع پیستون بستگی دارد. فرمول محاسبه سرعت به صورت زیر است
V=Q⁄A
که در آن: V سرعت (متر بر ثانیه)، Q دبی جریان هوا (متر مکعب بر ثانیه)، A سطح مقطع پیستون (متر مربع) هستند. دبی جریان هوا میتواند با توجه به مشخصات کمپرسور و سیستم لولهکشی محاسبه شود.
در کل سیلندرهای پنوماتیک اجزای حیاتی در بسیاری از سیستمهای صنعتی هستند. انتخاب مواد مناسب، رعایت استانداردهای تولید و انجام محاسبات دقیق نیرو و سرعت از جمله مواردی هستند که برای بهرهبرداری بهینه از این تجهیزات باید مورد توجه قرار گیرند. با درک عمیقتر از این مباحث، میتوان بهبودهای قابل توجهی در عملکرد و عمر مفید سیلندرهای پنوماتیک به دست آورد
جنس لوله های سیلندر پنوماتیک
جنس لولههای سیلندر پنوماتیک باید به گونهای انتخاب شود که ویژگیهایی مانند مقاومت در برابر خوردگی، سایش، فشار و حرارت را تامین کند.
متریالهای مختلفی برای ساخت این لولهها استفاده میشود که مهمترین آنها عبارتند از:
۱- آلومینیوم
مزایا: سبک وزن، مقاومت خوب در برابر خوردگی، قابلیت انتقال حرارت بالا.
کاربردها: معمولاً در سیلندرهای پنوماتیک استاندارد و عمومی به کار میرود.
۲- فولاد ضد زنگ
مزایا: مقاومت بسیار بالا در برابر خوردگی و سایش، مقاومت مکانیکی بالا.
کاربردها: در محیطهای خورنده و شرایط کاری سخت که نیاز به مقاومت بیشتری است.
۳- فولاد کربنی
مزایا: مقاومت مکانیکی بالا، قیمت مناسبتر نسبت به فولاد ضد زنگ.
معایب: مقاومت کمتر در برابر خوردگی نسبت به فولاد ضد زنگ.
کاربردها: در کاربردهای عمومی که شرایط محیطی خورنده نیست.
۴- برنز و برنج
مزایا: مقاومت خوب در برابر سایش و خوردگی، خاصیت خودروانکاری.
کاربردها: در برخی از سیلندرهای خاص و محیطهای ویژه که نیاز به این ویژگیها دارند.
۵- پلیمرها و پلاستیکهای مهندسی
مزایا: مقاومت بالا در برابر خوردگی، وزن سبک، قابلیت خودروانکاری.
معایب: مقاومت مکانیکی کمتر نسبت به فلزات.
کاربردها: در کاربردهای خاص و محیطهای خورنده که نیاز به مواد غیر فلزی است.
در کل انتخاب جنس لوله سیلندر پنوماتیک به عوامل مختلفی مانند نوع کاربرد، شرایط محیطی، فشار کاری و هزینه بستگی دارد. با توجه به این عوامل، میتوان متریال مناسب را انتخاب کرد تا عملکرد و دوام بهینهای برای سیلندر فراهم شود.
جنس شفت سیلندر پنوماتیک
جنس شفت سیلندر پنوماتیک باید ویژگیهای مهمی مانند مقاومت در برابر سایش، خوردگی، خمش و فشار را دارا باشد. انتخاب متریال مناسب برای شفت میتواند به بهبود عملکرد و افزایش عمر مفید سیلندر کمک کند.
متریالهای رایج برای ساخت شفت سیلندر پنوماتیک عبارتند از:
۱- فولاد کربنی سختکاری شده
مزایا: مقاومت بالا در برابر سایش و خمش، قابلیت تحمل فشارهای بالا.
معایب: مقاومت کمتر در برابر خوردگی نسبت به فولاد ضد زنگ.
کاربردها: معمولاً در کاربردهای عمومی و استاندارد به کار میرود.
۲- فولاد ضد زنگ (استنلس استیل)
مزایا: مقاومت بسیار بالا در برابر خوردگی، سایش و خمش، مناسب برای محیطهای خورنده.
معایب: قیمت بالاتر نسبت به فولاد کربنی.
کاربردها: در شرایط کاری سخت و محیطهای خورنده مانند صنایع شیمیایی و غذایی.
۳- فولاد کرومکاری شده
مزایا: سطح صاف و صیقلی با مقاومت بالا در برابر سایش، مقاومت متوسط در برابر خوردگی.
معایب: نیاز به نگهداری و پوشش مناسب برای جلوگیری از زنگزدگی در محیطهای خورنده.
کاربردها: در کاربردهای عمومی و صنعتی که نیاز به سطح صاف و مقاومت سایش بالا دارند.
۴- فولاد نیتروژن دهی شده
مزایا: مقاومت بسیار بالا در برابر سایش و خمش، سطح سخت و مقاوم.
معایب: فرآیند تولید پیچیدهتر و هزینه بالاتر نسبت به فولاد کربنی.
کاربردها: در شرایط کاری با فشار و سایش بالا که نیاز به مقاومت بیشتری است.
انتخاب جنس شفت به عوامل مختلفی مانند نوع کاربرد، شرایط محیطی، فشار کاری و هزینه بستگی دارد. برای کاربردهای عمومی و محیطهای غیر خورنده، فولاد کربنی سختکاری شده و فولاد کرومکاری شده انتخابهای مناسبی هستند. اما برای محیطهای خورنده و شرایط کاری سخت، فولاد ضد زنگ و فولاد نیتروژندهی شده ترجیح داده میشوند
جنس لوازم آب بند سیلندر های پنوماتیک
متریال لوازم آب بند سیلندر پنوماتیک لوازم آببند (Seals) در سیلندرهای پنوماتیک نقش حیاتی در جلوگیری از نشت هوا و حفظ فشار داخلی ایفا میکنند. متریالهای استفاده شده برای این لوازم باید دارای ویژگیهایی مانند مقاومت در برابر سایش، فشار، حرارت و مواد شیمیایی باشند.
برخی از متریالهای رایج برای لوازم آببند سیلندرهای پنوماتیک عبارتند از:
۱- نیتریل بوتادین رابر (NBR) یا نیتریل (Buna-N)
ویژگیها: مقاومت خوب در برابر روغنها، سوختها، و بسیاری از مواد شیمیایی، انعطافپذیری بالا، مقاومت در برابر سایش.
محدودیتها: تحمل حرارتی محدود (حداکثر تا حدود 100 درجه سانتیگراد).
کاربردها: در محیطهای در معرض تماس با روغن و گریس
۲- پلی اورتان (Polyurethane)
ویژگیها: مقاومت بسیار بالا در برابر سایش، انعطافپذیری خوب، مقاومت در برابر فشارهای بالا.
محدودیتها: مقاومت متوسط در برابر مواد شیمیایی.
کاربردها: در شرایطی که نیاز به مقاومت بالا در برابر سایش و فشار است
۳- فلوروکربن رابر (FKM) یا وایتون (Viton)
ویژگیها: مقاومت بسیار خوب در برابر حرارت (تا حدود 200 درجه سانتیگراد)، مواد شیمیایی و روغنها.
محدودیتها: قیمت بالاتر نسبت به نیتریل و پلییورتان.
کاربردها: در محیطهای با دمای بالا و تماس با مواد شیمیایی خورنده.
۴- پلیتترافلوئورواتیلن (PTFE) یا تفلون
ویژگیها: مقاومت بسیار بالا در برابر حرارت، مواد شیمیایی و سایش، خواص خودروانکاری.
محدودیتها: انعطافپذیری کمتر نسبت به لاستیکها.
کاربردها: در محیطهای با شرایط کاری سخت و مواد شیمیایی خورنده.
۵- سیلیکون رابر (Silicone Rubber)
ویژگیها: مقاومت بسیار خوب در برابر حرارت (تا حدود 200 درجه سانتیگراد)، انعطافپذیری بالا.
محدودیتها: مقاومت کمتر در برابر سایش و مواد شیمیایی.
کاربردها: در کاربردهای با دمای بالا و محیطهای بهداشتی
۶- ایتفیلون (Ethylene Propylene Diene Monomer – EPDM)
ویژگیها: مقاومت خوب در برابر آب، بخار و مواد شیمیایی غیر روغنی، انعطافپذیری خوب.
محدودیتها: مقاومت کمتر در برابر روغنها و هیدروکربنها.
کاربردها: در محیطهای با تماس با آب و بخار.
انتخاب متریال مناسب برای لوازم آببند بستگی به شرایط کاری، دمای عملیاتی، فشار، نوع سیال و میزان سایش دارد. با توجه به این عوامل، میتوان متریال مناسب را انتخاب کرد تا عمر مفید سیلندر پنوماتیک افزایش یابد و عملکرد بهینهای داشته باشد
شرکت فراز مهر ایرسا ایرسا از شرکت های معتبر که در زمینه فعالیت لوازم آب بند های هیدرولیک و پنوماتیک فعالیت می کند جهت اطلاعات بیشتر و سفارش لوازم آب بند به سایت این شرکت مرجعه نمایید .
تعمیرات و نگهداری سیلندر های پنوماتیک
برای افزایش طول عمر سیلندرهای پنوماتیک، میتوان از چندین روش و استراتژی استفاده کرد که به بهینهسازی عملکرد و کاهش سایش و خوردگی کمک میکنند. در زیر به برخی از مهمترین این روشها اشاره شده است
۱- نگهداری منظم و پیشگیرانه:
– برنامههای نگهداری منظم: اجرای برنامههای منظم برای بررسی و نگهداری سیلندرها شامل تمیزکاری، تعویض قطعات فرسوده و بررسی نشتیها.
روغنکاری: استفاده از روانکارهای مناسب و به موقع برای کاهش سایش و جلوگیری از زنگزدگی قطعات متحرک
۲- استفاده از مواد با کیفیت بالا:
– انتخاب متریال مناسب: استفاده از متریالهای با کیفیت و مقاوم در برابر سایش، خوردگی و حرارت برای قطعات مختلف سیلندر.
– استفاده از آببندهای با کیفیت: استفاده از آببندهای ساخته شده از مواد با دوام مانند نیتریل، پلییورتان یا وایتون که با شرایط کاری سازگار هستند
۳- کنترل کیفیت هوای فشرده:
– فیلتر کردن هوا ( واحد مراقبت پنوماتیک ): استفاده از فیلترهای مناسب برای جلوگیری از ورود ذرات آلاینده و رطوبت به داخل سیلندر.
– استفاده از خشککنها: به کارگیری خشککنها برای کاهش رطوبت هوا و جلوگیری از زنگزدگی داخلی سیلندرها . فیلتر های داخل واحد مراقبت ها از دو نوع فلزی و کاغذی می باشد
۴- تنظیمات صحیح سیلندر:
– تنظیم فشار کاری: اطمینان حاصل کردن از اینکه فشار هوای ورودی به سیلندر در محدوده توصیه شده قرار دارد تا از آسیبهای احتمالی جلوگیری شود.
– کنترل سرعت حرکت: استفاده از شیرهای کنترل دبی برای تنظیم سرعت حرکت سیلندر و جلوگیری از ضربههای ناگهانی
۵- طراحی و نصب صحیح:
– طراحی مناسب سیستم: طراحی سیستم پنوماتیک به گونهای که بارها به صورت متوازن توزیع شوند و از ایجاد نیروهای اضافی روی سیلندر جلوگیری شود.
– نصب صحیح سیلندر: اطمینان حاصل کردن از نصب صحیح سیلندر و جلوگیری از انحراف محوری که میتواند باعث سایش و خوردگی شود
۶- بازرسی و تعویض قطعات فرسوده:
– بررسی دورهای قطعات: بررسی دورهای قطعات داخلی و خارجی سیلندر و تعویض قطعات فرسوده مانند آببندها، شفتها و بوشها.
– استفاده از کیتهای تعمیر و نگهداری: استفاده از کیتهای تعمیر و نگهداری که شامل قطعات یدکی و آببندهای مورد نیاز برای تعمیرات سریع و موثر هستند
۷- آموزش و آگاهی کارکنان:
– آموزش کارکنان: آموزش کارکنان درباره نحوه صحیح استفاده، نگهداری و تعمیر سیلندرهای پنوماتیک.
– افزایش آگاهی: افزایش آگاهی کارکنان درباره اهمیت نگهداری و روشهای جلوگیری از خرابیهای احتمالی
۸- استفاده از تجهیزات پیشرفته:
– نظارت خودکار: استفاده از سیستمهای نظارت خودکار برای مانیتورینگ عملکرد سیلندرها و شناسایی مشکلات قبل از وقوع خرابی.
– تحلیل دادهها: تحلیل دادههای عملکردی برای شناسایی الگوهای خرابی و بهبود فرآیندهای نگهداری.
با رعایت این نکات و استراتژیها میتوان به طور موثر طول عمر سیلندرهای پنوماتیک را افزایش داد و از خرابیهای ناگهانی و هزینههای اضافی جلوگیری کرد
سایز شیلنگ های پنوماتیک از شیر های پنوماتیک به سیلندر چگونه انتخاب شود ؟
انتخاب سایز مناسب شیلنگهای پنوماتیک برای اتصال شیرهای پنوماتیک به سیلندرها اهمیت زیادی دارد، زیرا این امر میتواند بر عملکرد سیستم تأثیر بگذارد. عواملی که در انتخاب سایز شیلنگ باید در نظر گرفته شوند عبارتند از:
۱- فشار کاری سیستم محدوده فشار کاری: اطمینان حاصل کنید که شیلنگ انتخابی بتواند فشار کاری سیستم را تحمل کند. شیلنگها معمولاً بر اساس حداکثر فشار کاری مشخص میشوند
۲- دبی جریان هوا مقدار دبی هوا (Flow Rate): سایز شیلنگ باید به گونهای باشد که دبی جریان هوا را بدون افت فشار زیاد تأمین کند. افت فشار زیاد میتواند عملکرد سیلندر را کاهش دهد. میتوانید از جداول یا نرمافزارهای مخصوص برای محاسبه افت فشار در شیلنگها بر اساس طول و قطر شیلنگ استفاده کنید
۳- طول شیلنگ طول شیلنگ: هرچه طول شیلنگ بیشتر باشد، افت فشار نیز بیشتر خواهد بود. برای کاهش افت فشار، در صورت نیاز به استفاده از شیلنگهای بلند، میتوان از قطرهای بزرگتر استفاده کرد
۴- قطر داخلی شیلنگ: قطر داخلی شیلنگ باید به گونهای انتخاب شود که جریان هوا به طور مطلوب عبور کند. جدولهای استاندارد میتوانند در تعیین قطر مناسب کمک کنند.
۵- اندازه پورتهای شیر و سیلندر: اندازه پورتهای ورودی و خروجی شیر و سیلندر نیز باید با قطر داخلی شیلنگ همخوانی داشته باشد تا جریان هوا به درستی منتقل شود.
۶- میزان مقاومت شیلنگ در برابر شرایط محیطی: در نظر گرفتن شرایط محیطی مانند دما، رطوبت، و حضور مواد شیمیایی که ممکن است بر عمر و عملکرد شیلنگ تأثیر بگذارد
۷- نوع کاربرد: در کاربردهایی که نیاز به دقت بالا و کنترل سرعت است، افت فشار و تاثیر آن بر عملکرد سیلندر بیشتر مورد توجه قرار میگیرد. در اینجا با یک مثال کاربردی به شرح بیشتر این مورد میپردازیم:
فرض کنید شما یک سیستم پنوماتیک با فشار کاری 6 بار دارید و میخواهید یک شیر پنوماتیک با پورت 1/4 اینچ را به یک سیلندر پنوماتیک متصل کنید. لازم است برای این کار محاسبات زیر را انجام دهید:
۱- محاسبه دبی هوا: با توجه به مشخصات سیلندر و شیر، دبی هوا را محاسبه کنید. فرض کنیم دبی هوا 100 لیتر در دقیقه (L/min) باشد.
۲- انتخاب قطر شیلنگ: با استفاده از جداول استاندارد، برای دبی هوا و طول شیلنگ مورد نظر، قطر داخلی شیلنگ را انتخاب کنید. مثلاً برای دبی 100 L/min و طول 2 متر، قطر داخلی 8 میلیمتر میتواند مناسب باشد.
۳- مقایسه با اندازه پورتها: مطمئن شوید که اندازه پورتهای شیر و سیلندر با قطر شیلنگ انتخابی همخوانی دارند. در این مثال، پورتهای 1/4 اینچ معمولاً با شیلنگهای 6 تا 8 میلیمتر سازگار هستند.
نتیجهگیری: برای انتخاب سایز مناسب شیلنگهای پنوماتیک، توجه به فشار کاری، دبی جریان هوا، طول شیلنگ، قطر داخلی شیلنگ، اندازه پورتهای شیر و سیلندر، شرایط محیطی و نوع کاربرد ضروری است. با رعایت این نکات، میتوانید از عملکرد بهینه و طول عمر بیشتر سیستم پنوماتیک خود اطمینان حاصل کنید .